blokenoname
DIY Log Dabbler 😁🪵💪💨💨💨
So! Tested out the star washer base with the 11mm UD tubing. Worked out reasonably well for a prototype. Tried to pull it apart with considerable force applied; even threw it against the wall... mechanical connection holds up! 

Used an M10 external star washer here with an ID of 10.5mm to 10.77mm. It's about 0.9mm thick and has an OD of ~18mm.
Procedure is basically the same as working with the flat M10 washer I'm usually using for fastening the 11mm OD heater cover. Bit less trimming of the tube necessary here , as ID tolerances of the star washer seem to be less strict than for the flat washers. Meaning... didn't even need to fire up the bench grinder here, but simply used a big hand-file for a minute or two, until I could feed the tube into the washer's hole and give it a go with the hammer.
Also... the nudges of the star washer are a perfect fit for my M3/16mm round head wood screws


Used an M10 external star washer here with an ID of 10.5mm to 10.77mm. It's about 0.9mm thick and has an OD of ~18mm.
Procedure is basically the same as working with the flat M10 washer I'm usually using for fastening the 11mm OD heater cover. Bit less trimming of the tube necessary here , as ID tolerances of the star washer seem to be less strict than for the flat washers. Meaning... didn't even need to fire up the bench grinder here, but simply used a big hand-file for a minute or two, until I could feed the tube into the washer's hole and give it a go with the hammer.
Also... the nudges of the star washer are a perfect fit for my M3/16mm round head wood screws

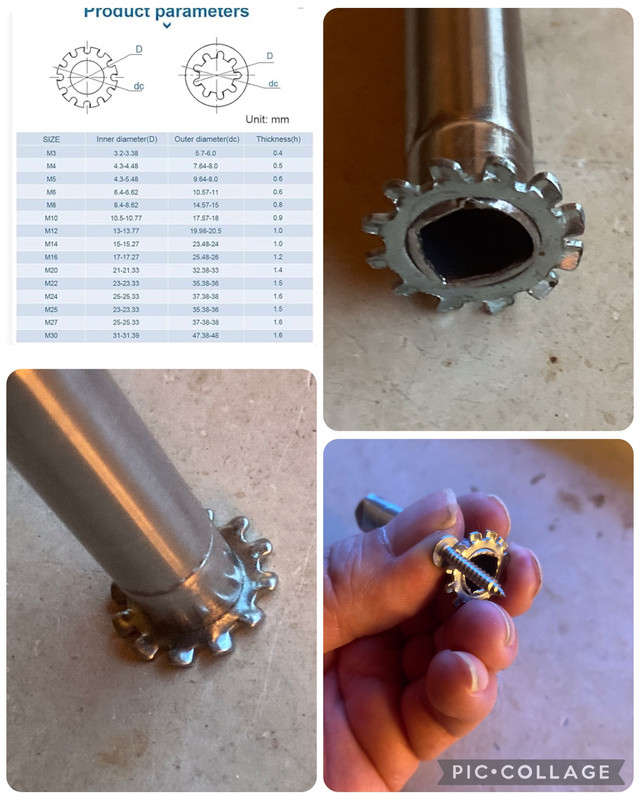
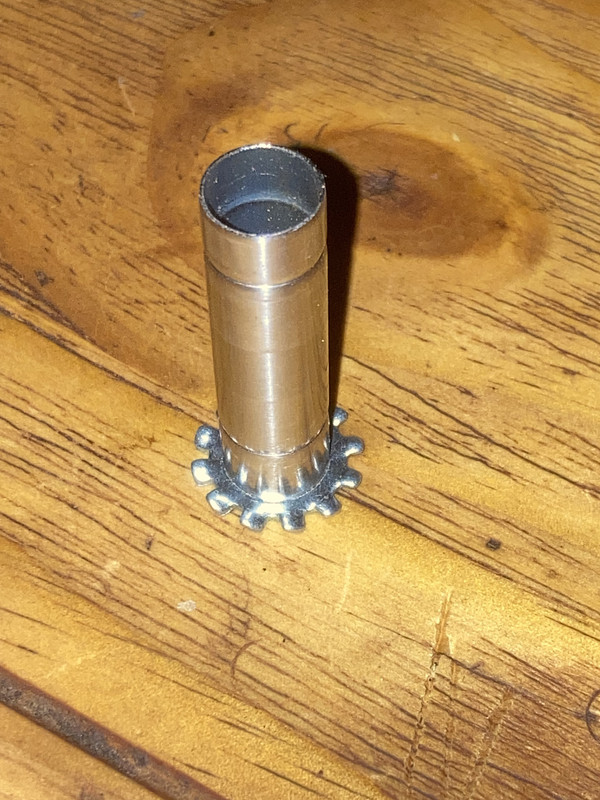
Last edited: