Stoomboot
Well-Known Member
Hi FC members,
A few months ago, a friend and I decided we wanted to build a DIY temperature controlled vaporizer. We drew up a few designs but none of them where satisfying. When we came across this tread while trying to find inspiration, we were imminently convinced of the Bud Toaster design. Although our version is far from finished I still would like to share our progressions so far.
Sooo, we started building our first prototype (witch is almost finished now). We ordered parts and started building/experimenting. I think pictures can explain this best
.
The 'don't blow on it or it will break' setup:
A holder that is a little bit sturdier :
And the (messy) electronics as they are now:
Bigger oventube (We first ordered 12mm 'bud tubes' but they didn't fit into the 16mm oventubes we also orderd. We are now using a 20mm oventube)
And some LED madness
As you can see we did a few things different. We wanted to use a lead acid battery so we designed the electronics around 12 volt. We used a thinner nichrome heater coil to get more heat with less current. And we also used 7 segment displays instead of a separate thermometer.
A small list of electronics that we are using:
The microcontroller is programmed in C and uses a PID loop to control the temperature. If someone is interested I will upload the code somewhere.
There are a few thing we still need / want to do.
As you can see, it is all still far away from something you can call aesthetically pleasing but its getting there
.
We already 'tested' it a few times and we are amazed with how well it works. So a big thanks to Hippy Dick and all other contributors. It is amazing to see that people form all over the world are sharing info to make some awesome stuff (and maybe get a bit high in the process
).
Happy vaping,
-Stoomboot & Co
A few months ago, a friend and I decided we wanted to build a DIY temperature controlled vaporizer. We drew up a few designs but none of them where satisfying. When we came across this tread while trying to find inspiration, we were imminently convinced of the Bud Toaster design. Although our version is far from finished I still would like to share our progressions so far.
Sooo, we started building our first prototype (witch is almost finished now). We ordered parts and started building/experimenting. I think pictures can explain this best

The 'don't blow on it or it will break' setup:


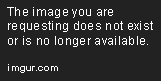

A holder that is a little bit sturdier :

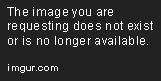

And the (messy) electronics as they are now:


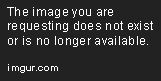
Bigger oventube (We first ordered 12mm 'bud tubes' but they didn't fit into the 16mm oventubes we also orderd. We are now using a 20mm oventube)


And some LED madness


As you can see we did a few things different. We wanted to use a lead acid battery so we designed the electronics around 12 volt. We used a thinner nichrome heater coil to get more heat with less current. And we also used 7 segment displays instead of a separate thermometer.
A small list of electronics that we are using:
- The Atmel Atmega 328P microcontroller (I had it laying around so I used it)
- 3 seven segment displays
- A rotary encoder
- International Rectifier IRF3707S MOSFET
- 0.80 mm nichrome wire
- NXP KTY 84-130 silicone based temperature sensor
- M74HC595B1R shift register (to drive the display)
The microcontroller is programmed in C and uses a PID loop to control the temperature. If someone is interested I will upload the code somewhere.
There are a few thing we still need / want to do.
- Build a new case
- Finish battery protection (almost done, I only need to make the readings more accurate)
- Make temperature control more stable (currently at +/- 3 degrees C)
As you can see, it is all still far away from something you can call aesthetically pleasing but its getting there

We already 'tested' it a few times and we are amazed with how well it works. So a big thanks to Hippy Dick and all other contributors. It is amazing to see that people form all over the world are sharing info to make some awesome stuff (and maybe get a bit high in the process

Happy vaping,
-Stoomboot & Co