Hey Guys/Gals.
Opening this thread to have a spot to discuss and pool our knowledge regarding best firmware options to alter existing box mods to better suit our vaping needs. There seems to be more and more 510 based vaporizers coming to market in our world here. The TC technology is still new for our application but has being close to perfected for the needs of ECig users.
So far, the "myevic" open source firmware seems to be a big topic as has very complicated and powerful upgrades for user accessibility to setups and alterations. We need to take advantage of the firmware to make these devices do our bidding.
The reason is they all have the same chip set and the code has been leaked out and now open source.
This chip set has proven to work well for our purposes. The newest firmware even allows for PID alterations of the heat up algorithm. The customized firmware is in a file called myevic.bin and is being changed regularly. Advanced options like 15 second time out is a nice option. The same file works on all the above compatible mods.
For information and menu instructions go here.
For the actual file and some history go here.
The way this firmware works well for the Project is:
Relevant Firmware Settings:
For realistic numbers up .56 ohm to .600 ohm for starting point and calibrate further later. Raising this number for hotter and lower for cooler. Turn Check to “off”. Zero all will force a re-read of actual ohms.
Note that manual entered ohms must be within 10% of actual read ohms or settings will change back when used. Including the check to “on”.
Don’t forget to turn the temp down to around 380F after you manually upped the ohms.
After you alter the ohms by adding .04 ohms, the TCR should be changed to 170 to help the temperature hold linearly true.
Set up 15 second timeout. To avoid hot preheat turn Algo to PID and change numbers as shown. This setting prevents preheat and ensures minimal charring. If Algo is off, expect 1-2 seconds of preheat. Changing these numbers will also affect the overall temperature and re-doing ohms calibration will be necessary.
Access this setting if going to use NFE software.
I also now own a couple DNA units and really, really love them.
The DNA chipset seems to handle a broader range of builds in a more stable manor. Maybe it's the sample rate or preset PID might have a more intelligent algorithm..? Not clear but the monitor graphing is generally spot on when using the software to see whats happening.
What makes it really cool is the way you alter the TCR number. Not restricted to just altering the slope from room temperature to the end of the scale. But can change two spots along the curve to change the linearity of the curve. In fact the change is done in a dragging the points in a visual graph. The preheat is adjustable by stating how much, and for how long in drop down boxes. All done within Escribe software. Check out the demo.
Now the "myevic" can be adjusted to be very close in performance, it's the PID to match your specific build is the key. Playing with the PID (Proportional, Integral, Derivative) can be a bitch but fruitful when you get it right.
I do believe the EVic stock had the preheat a little high but also remember it seemed different with each firmware release. As with TCR presets.
Here is a screen shot from inside the Escribe software. I set up a material called Project and adjusted the points to get the result I wanted. Altering the first two point adjusted the offset for scaling. Adjusting the third number is the critical one. It's how the temp changes from room temperature to the upper temp you ever plan to use. It this case 450F. The last point is set a minimal difference from the max usable to prevent the unit from running the temp a way too hot. Gotta love that part.
The DNA devices have come down to reasonable prices now so don't be shy. Also, the material files are of course transferable.
Fun Stuff, let get the discussion going...

Opening this thread to have a spot to discuss and pool our knowledge regarding best firmware options to alter existing box mods to better suit our vaping needs. There seems to be more and more 510 based vaporizers coming to market in our world here. The TC technology is still new for our application but has being close to perfected for the needs of ECig users.
So far, the "myevic" open source firmware seems to be a big topic as has very complicated and powerful upgrades for user accessibility to setups and alterations. We need to take advantage of the firmware to make these devices do our bidding.
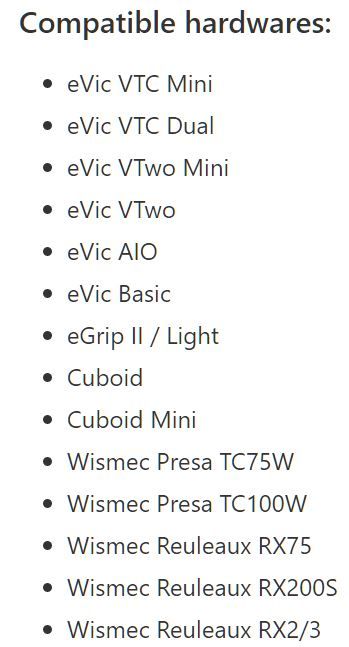
The reason is they all have the same chip set and the code has been leaked out and now open source.
This chip set has proven to work well for our purposes. The newest firmware even allows for PID alterations of the heat up algorithm. The customized firmware is in a file called myevic.bin and is being changed regularly. Advanced options like 15 second time out is a nice option. The same file works on all the above compatible mods.
For information and menu instructions go here.
For the actual file and some history go here.
The way this firmware works well for the Project is:
Relevant Firmware Settings:
For realistic numbers up .56 ohm to .600 ohm for starting point and calibrate further later. Raising this number for hotter and lower for cooler. Turn Check to “off”. Zero all will force a re-read of actual ohms.
Note that manual entered ohms must be within 10% of actual read ohms or settings will change back when used. Including the check to “on”.
Don’t forget to turn the temp down to around 380F after you manually upped the ohms.
After you alter the ohms by adding .04 ohms, the TCR should be changed to 170 to help the temperature hold linearly true.
Set up 15 second timeout. To avoid hot preheat turn Algo to PID and change numbers as shown. This setting prevents preheat and ensures minimal charring. If Algo is off, expect 1-2 seconds of preheat. Changing these numbers will also affect the overall temperature and re-doing ohms calibration will be necessary.
Access this setting if going to use NFE software.
I also now own a couple DNA units and really, really love them.
The DNA chipset seems to handle a broader range of builds in a more stable manor. Maybe it's the sample rate or preset PID might have a more intelligent algorithm..? Not clear but the monitor graphing is generally spot on when using the software to see whats happening.
What makes it really cool is the way you alter the TCR number. Not restricted to just altering the slope from room temperature to the end of the scale. But can change two spots along the curve to change the linearity of the curve. In fact the change is done in a dragging the points in a visual graph. The preheat is adjustable by stating how much, and for how long in drop down boxes. All done within Escribe software. Check out the demo.
Now the "myevic" can be adjusted to be very close in performance, it's the PID to match your specific build is the key. Playing with the PID (Proportional, Integral, Derivative) can be a bitch but fruitful when you get it right.
I do believe the EVic stock had the preheat a little high but also remember it seemed different with each firmware release. As with TCR presets.
Here is a screen shot from inside the Escribe software. I set up a material called Project and adjusted the points to get the result I wanted. Altering the first two point adjusted the offset for scaling. Adjusting the third number is the critical one. It's how the temp changes from room temperature to the upper temp you ever plan to use. It this case 450F. The last point is set a minimal difference from the max usable to prevent the unit from running the temp a way too hot. Gotta love that part.
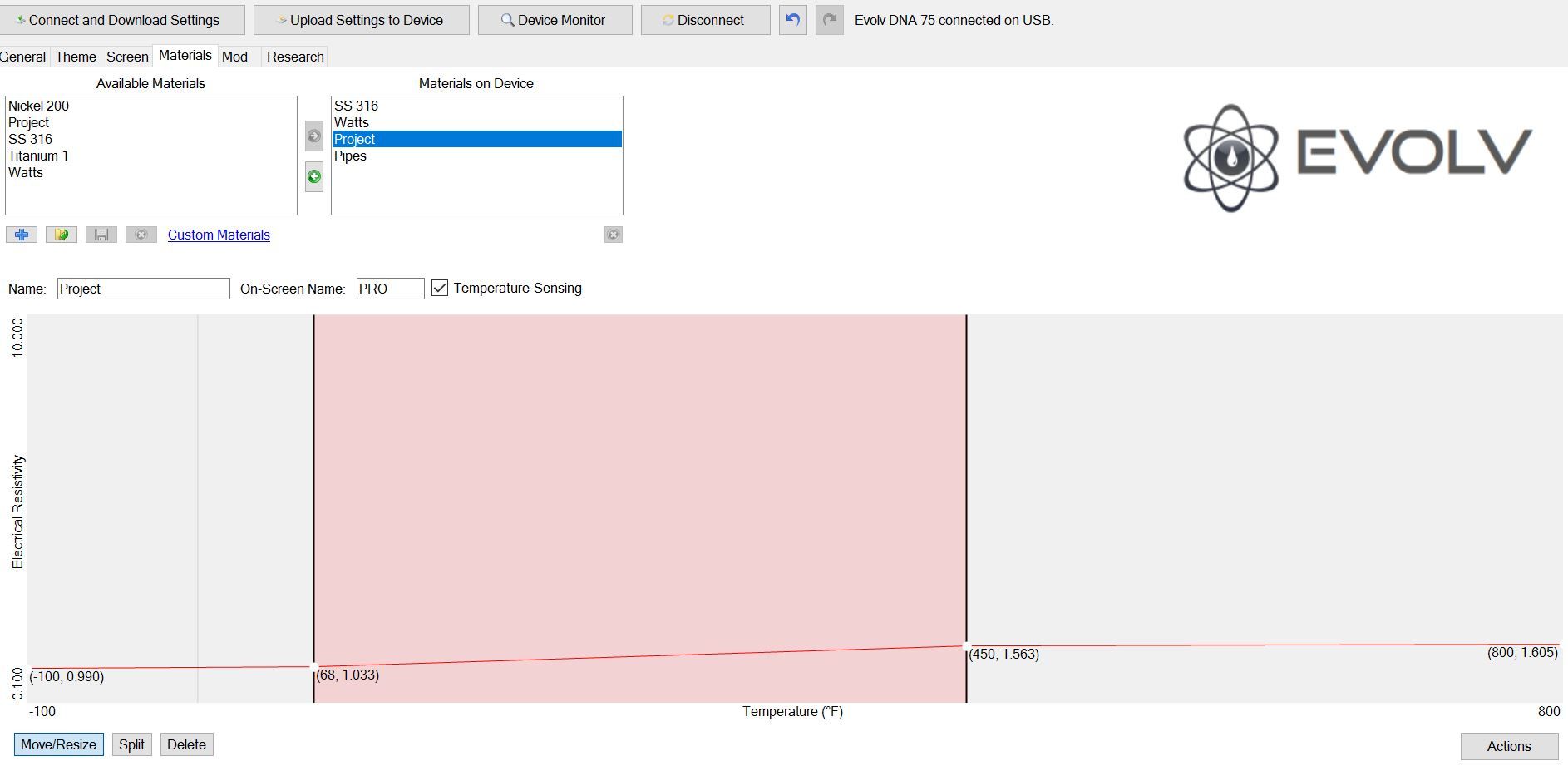
The DNA devices have come down to reasonable prices now so don't be shy. Also, the material files are of course transferable.
Fun Stuff, let get the discussion going...

Last edited: