how are these cleaning plugs different from silicone rubber stoppers that are made to plug ground glass joints...?
not knocking your product, but rubber stoppers can be found very cheap and in all sizes available. ive been using them to clean my glass for years.
No offense taken

First, my cleaning plugs are made from non-toxic materials - aquarium silicon sealant and corn starch. Sure it's used for cleaning, but I'm still not taking any chances. If I wanted to be cheap, I could have used traditional 100% silicon sealant from walmart for $3 a tube. Even when cured, those plugs might contain some trace toxic chemicals from the curing of the silicon. I don't know for sure about traditional rubber stoppers, but I'm sure they're probably fine after a good rinse. I'm sure both traditional stoppers and my tapered plugs would be safe to use in this respect.
However, since I'm making them from silicon sealant, they are much more flexible than those rubber stoppers. If you look at the plug for the mouthpiece of the D020, it's flexed down the shaft at an angle. You can literally bend these plugs in half and they will spring back to their normal shape. The material is really quite something (My friend tells me I should start selling my own sex toys, ha ha ha)
If you've never made some of this stuff, I suggest you try. Add a scoop of corn starch to 100% clear silicon and mix thoroughly. It's really an awesome material for making flexible water tight things (google search "Oogoo") - however please mix outside, the off-gassing while mixing can be quite strong (extreme vinegar smell)
Lastly, the model I'm currently listing has gone through 3 different versions to reach a size which fits multiple common sizes used on my glass pieces (14mm female GONG, 18mm female GONG, and D020 Mouthpiece).
And as stated, I made a size which fits my needs for the various sizes I have. But since it's a 3D design, I can simply adjust the parameters for the desired size print a new mold for anyone who needs something different. I'm also considering to sell the molds themselves on my shop at some point in the near future.
I've been studying wine cork stoppers recently and thinking about tweaking my model a bit to mimic some of the more efficient designs. I'll keep you guys posted.

------------------------------------------------------
Changing subjects. I recently fired up my 3D scanner for the first time!! The scanning process is quite tedious for my underpowered 6 year old laptop, patience is quite a virtue. But it works!
Here's a screenshot of my first full color 3D scan! Only slightly edited to solidify the model (Trimmed the bottom since only wanted a scan of the bottom half of the ascent). Once I've cleaned up the model a bit (running through some filters), I'm going to design a Davinci Ascent charging dock by digitally 'subtracting' the 3D scan from my design, creating a (hopefully) perfect fit.
According to the digital measurements, it looks like I'm within 0.5 mm of the exact dimensions I need for a perfect fit. Not bad for my first ever 3D scan!
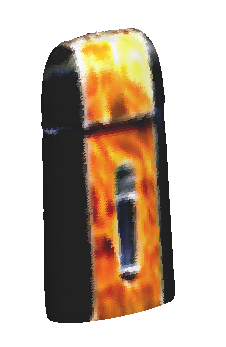
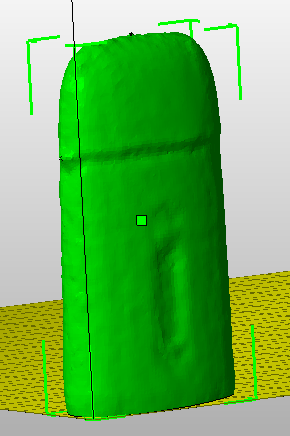
--------------------------
Also note - BLACK plastic is now back in stock. I'll be uploading some new black Davinci Ascent stands and tampers to the etsy store next week
Last edited by a moderator: