Rick
Zapman
OK, over with the suspense. I suppose if I were smarter(in some way), I would just let this ride for awhile to keep us 'up there' with the stars. I have already let this go long enough. It is fun to see all the comments and guesses and Vitolos gizmo actually gives me an intro.
We are still simple, very simple around here so our new design is nothing really new except for the way it is built.
When we got to know Bob, one of our wood suppliers(Walnut) a bit better, he started showing us around his entire shop area which I am guessing is several acres of buildings. He made his fortune inventing, patenting and manufacturing boat accessories. Lifts, jacks and all the stuff the guys with the pleasure boats need to have all the bells and whistles.
One day early this spring he shows us a machine that is cutting 1" stainless steel plate with water. A 55,000 PSI water jet, all computerized. He has all the machine shop tools to do just about anything, including a plating shop. And he specializes in Stainless Steel.
So I take him in a Zap heatport a couple months ago and ask "can you make me this out of SS". He laughs. "Are you kidding? You should not be wasting your time making those". "Besides, we can do this and this and this........."
So his head machinist, another Rick coincidentally, has been tweaking a design for the last month. Then testing here at Zapville, a little more tweaking and we are due next Tuesday for what we think will be the final prototype.
Our new heatport, or heat exchanger if you prefer, is turned from a solid chunk of 1" round SS stock. No tubing, no washers, no springs and pins, no soldering(only welding) no top retaining clip as the central heat transfer unit is tack welded to the SS heatport liner. All one piece when finished with the final step being an electro polishing process that shines up the entire assembly, inside and out, welds and all, to a brilliant, polished, SS look. Bob tells me it is the same process used for surgical grade instruments.
The entire assembly is then pressed into the wood with an interference fit. As soon as the heat goes on, it tightens even more as the center hole in the wood actually shrinks as soon as the Zap comes on the first time.
All the proto and design work was/is on Bob. That is what made all this possible. I do not have my final cost per unit yet but I have been assured it will be in my current range for heatport cost of production. Much of my current cost is my time as there is a fair amount of labor involved making the current version. My out of pocket cash outlay will be more for the SS design but my Zap making time will be cut 20 minutes to 1/2 hour per unit. That will make for even quicker delivery times than we currently strive for.
I'll leave us with a couple pics. Top view and bottom view. Both views show the three main pieces to the left and the completed unit on the right. There is a SS screen in the center bored hole. The center machined section fits tight at the top AND the bottom of the SS sleeve so there can be no movement between the two. Four tack welds hold the center section to the sleeve. The small round top portion is welded to the top of the center unit with the SS screen sandwiched between the two before welding.
The stem tip fit in the center heatport hole is exact. No wobble.
This is a fully machined and professionally built heatport/heat exchanger. It is made locally by local folks(project 420 even!) and finished to surgical grade specs.
We should be in full production by the end of next week, assuming our final tweaks do not make it run TOO hot. Proto #2 in the pictures is running plenty hot.
I expect plenty of questions about details of this change in design that I have not yet addressed. I actually still have some questions myself that can only be answered with a bit more time.
We are still simple, very simple around here so our new design is nothing really new except for the way it is built.
When we got to know Bob, one of our wood suppliers(Walnut) a bit better, he started showing us around his entire shop area which I am guessing is several acres of buildings. He made his fortune inventing, patenting and manufacturing boat accessories. Lifts, jacks and all the stuff the guys with the pleasure boats need to have all the bells and whistles.
One day early this spring he shows us a machine that is cutting 1" stainless steel plate with water. A 55,000 PSI water jet, all computerized. He has all the machine shop tools to do just about anything, including a plating shop. And he specializes in Stainless Steel.
So I take him in a Zap heatport a couple months ago and ask "can you make me this out of SS". He laughs. "Are you kidding? You should not be wasting your time making those". "Besides, we can do this and this and this........."
So his head machinist, another Rick coincidentally, has been tweaking a design for the last month. Then testing here at Zapville, a little more tweaking and we are due next Tuesday for what we think will be the final prototype.
Our new heatport, or heat exchanger if you prefer, is turned from a solid chunk of 1" round SS stock. No tubing, no washers, no springs and pins, no soldering(only welding) no top retaining clip as the central heat transfer unit is tack welded to the SS heatport liner. All one piece when finished with the final step being an electro polishing process that shines up the entire assembly, inside and out, welds and all, to a brilliant, polished, SS look. Bob tells me it is the same process used for surgical grade instruments.
The entire assembly is then pressed into the wood with an interference fit. As soon as the heat goes on, it tightens even more as the center hole in the wood actually shrinks as soon as the Zap comes on the first time.
All the proto and design work was/is on Bob. That is what made all this possible. I do not have my final cost per unit yet but I have been assured it will be in my current range for heatport cost of production. Much of my current cost is my time as there is a fair amount of labor involved making the current version. My out of pocket cash outlay will be more for the SS design but my Zap making time will be cut 20 minutes to 1/2 hour per unit. That will make for even quicker delivery times than we currently strive for.
I'll leave us with a couple pics. Top view and bottom view. Both views show the three main pieces to the left and the completed unit on the right. There is a SS screen in the center bored hole. The center machined section fits tight at the top AND the bottom of the SS sleeve so there can be no movement between the two. Four tack welds hold the center section to the sleeve. The small round top portion is welded to the top of the center unit with the SS screen sandwiched between the two before welding.
The stem tip fit in the center heatport hole is exact. No wobble.
This is a fully machined and professionally built heatport/heat exchanger. It is made locally by local folks(project 420 even!) and finished to surgical grade specs.
We should be in full production by the end of next week, assuming our final tweaks do not make it run TOO hot. Proto #2 in the pictures is running plenty hot.
I expect plenty of questions about details of this change in design that I have not yet addressed. I actually still have some questions myself that can only be answered with a bit more time.
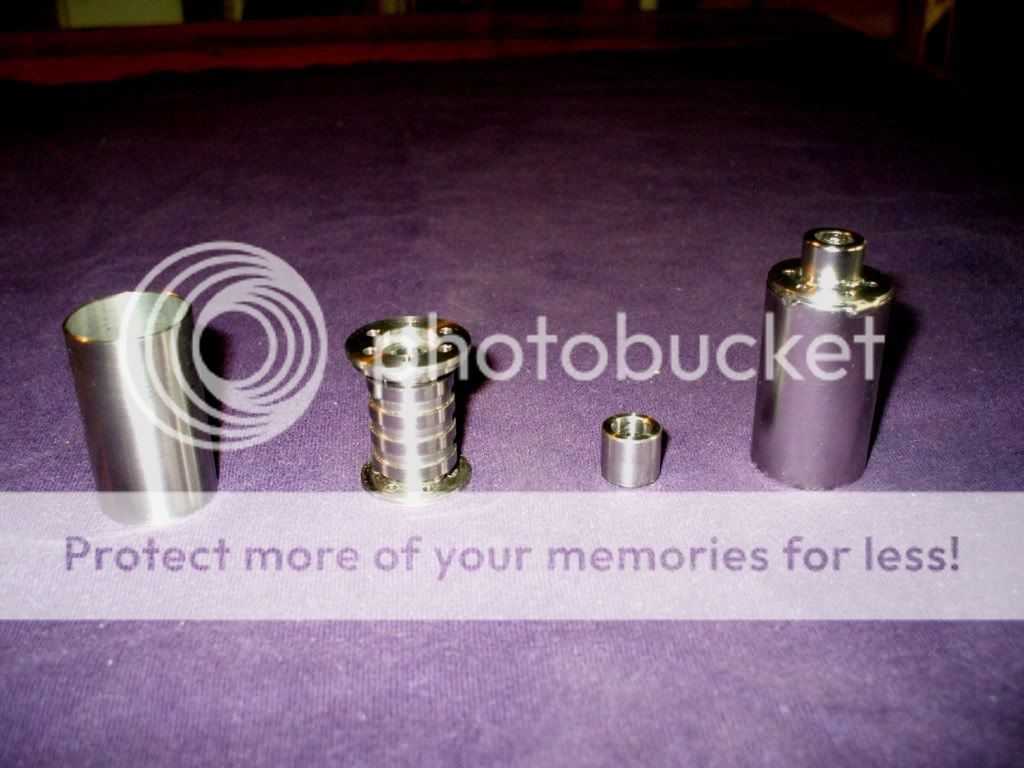
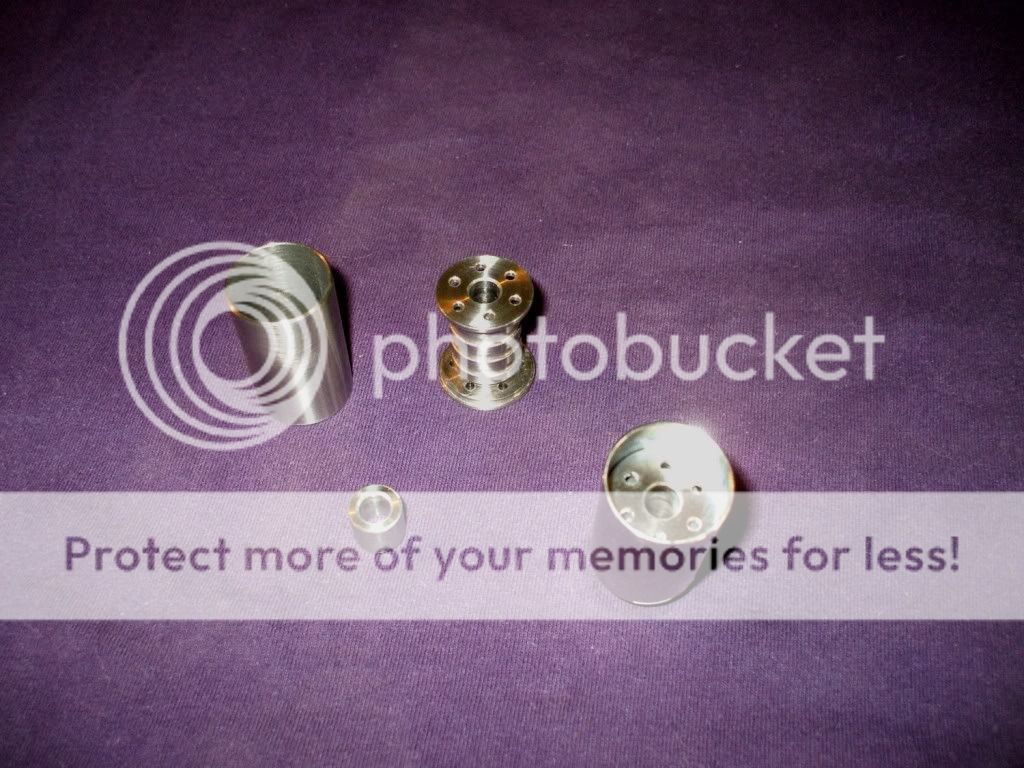