There have been some questions as to how the new style log vaporizers operate. I am posting this in the vaporization discussion section since it is not model specific. There are multiple vaporizers that use this technology.
The following diagram illustrates how this new technology works. It also provides terminology for each of the parts.
There are three main parts. The core outer tube, the core center tube, and the heating element.
The roasting tubes can be placed over the core center tube or into the core center tube to draw hot air through the herbal mass. Room air enters into the space between the core outer and center tubes traveling down to the bottom. The air passes through holes drilled into the center tube and makes a 180 degree turn passing between the center tube and the heating element.
The heart of the system is a heating element. The HI uses a vitrious enamel coated resistor that is identical to those found in the heart of all 12 volt log vaporizers. It is about 5mm in diameter and 23mm in length. The temperature measured 450F with a probe in contact with both the center tube and heating element with 12 volts applied. Since the HI is able to cause combustion at 12 volts and combustion occurs at around 450F, therefore the temperature of the air leaving the center tube is approximately the same as the temperature of the heating element. If the heating element can reach 700F, then the air coming out will be 700F. The reason for this is the holes drilled into the center tube. They provide a physical break in the metal which significantly reduces the metal conduction path. They are the real key to the design. The holes eliminate 2/3 of the metal conduction path with the HI. The heat is mostly trapped in the center tube. The total area of all the holes (6) in the HI center tube is equivalent to the area of the center tube so the holes do not provide any additional resistance to air flow. The only air flow resistance is from the heating element in the center tube. The longer the heating element and center tube, the more air resistance. Only the portion of the heating element in the air stream will transfer heat to the air. Having a heating element with 4 times more surface area stuck into the core will not transfer more heat since only the portion in the air stream can transfer heat to the air stream. The distance from the holes in the center tube to the top of the center tube will determine both the air resistance and how much heat can be transferred to the air. This distance is 30mm with the HI.
The HI center tube is made from stainless steel which has a thermal conductivity of about 20 (Btu/(hr oF ft)). The HI outer tube is also made from stainless steel. I had considered using aluminum since it is easier to work, but it has a thermal conductivity of about 120 (Btu/(hr oF ft)) which is 6 times higher than stainless steel. I want the heat to stay at the center tube so that it is available to heat the air rather than conducting the heat away and into the wood. Bare aluminum also has a nasty habit of forming an oxide layer which could make the outer tube larger in diameter and crack the wood over time. Stainless steel remains very stable and is much stronger.
I also measured a surface contact temperature of 285F at the core outer tube with 12 volts applied to the HI. Since the heat conduction path is severely limited, there will be much less heat transferred to the wood which will eliminate any charring concerns.
The following diagram illustrates how this new technology works. It also provides terminology for each of the parts.
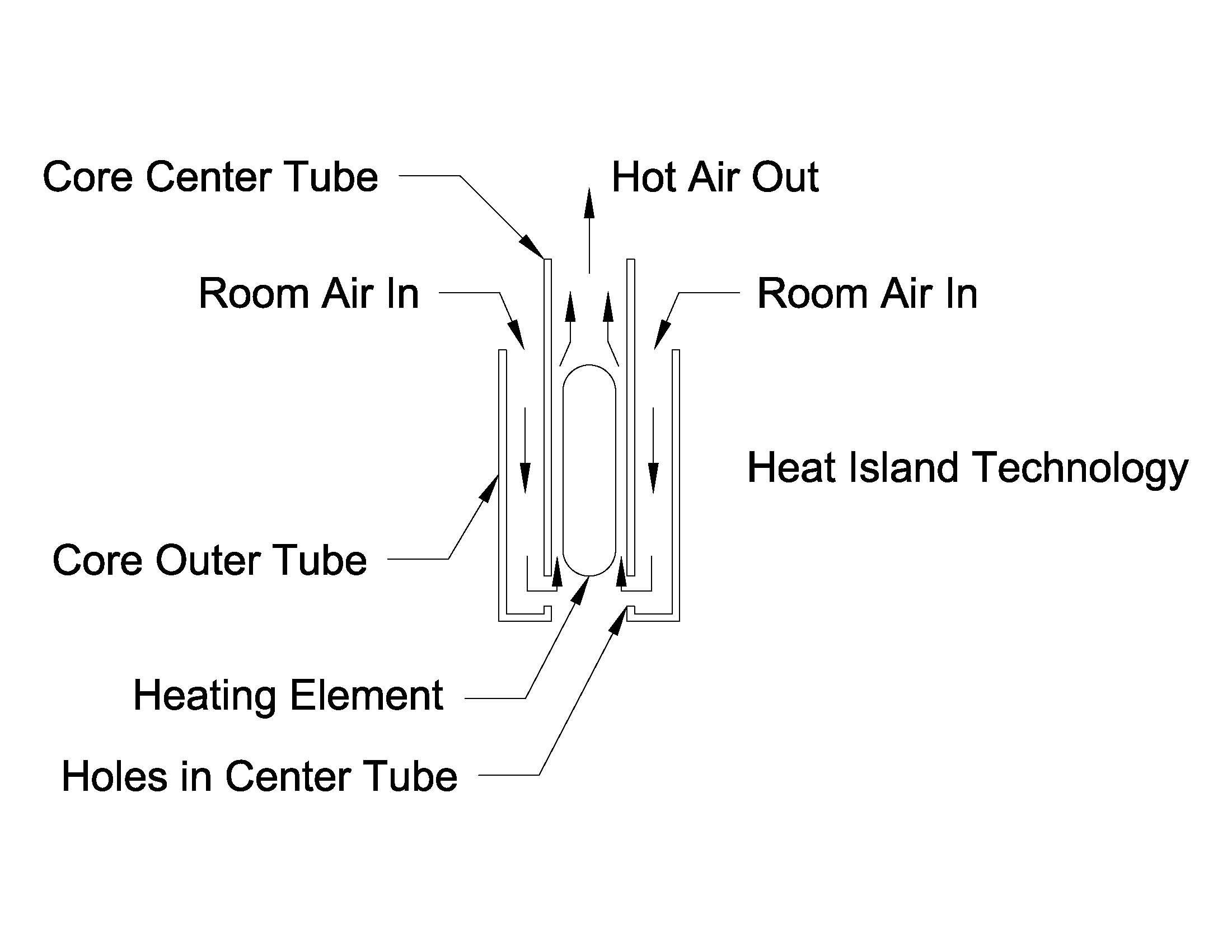
There are three main parts. The core outer tube, the core center tube, and the heating element.
The roasting tubes can be placed over the core center tube or into the core center tube to draw hot air through the herbal mass. Room air enters into the space between the core outer and center tubes traveling down to the bottom. The air passes through holes drilled into the center tube and makes a 180 degree turn passing between the center tube and the heating element.
The heart of the system is a heating element. The HI uses a vitrious enamel coated resistor that is identical to those found in the heart of all 12 volt log vaporizers. It is about 5mm in diameter and 23mm in length. The temperature measured 450F with a probe in contact with both the center tube and heating element with 12 volts applied. Since the HI is able to cause combustion at 12 volts and combustion occurs at around 450F, therefore the temperature of the air leaving the center tube is approximately the same as the temperature of the heating element. If the heating element can reach 700F, then the air coming out will be 700F. The reason for this is the holes drilled into the center tube. They provide a physical break in the metal which significantly reduces the metal conduction path. They are the real key to the design. The holes eliminate 2/3 of the metal conduction path with the HI. The heat is mostly trapped in the center tube. The total area of all the holes (6) in the HI center tube is equivalent to the area of the center tube so the holes do not provide any additional resistance to air flow. The only air flow resistance is from the heating element in the center tube. The longer the heating element and center tube, the more air resistance. Only the portion of the heating element in the air stream will transfer heat to the air. Having a heating element with 4 times more surface area stuck into the core will not transfer more heat since only the portion in the air stream can transfer heat to the air stream. The distance from the holes in the center tube to the top of the center tube will determine both the air resistance and how much heat can be transferred to the air. This distance is 30mm with the HI.
The HI center tube is made from stainless steel which has a thermal conductivity of about 20 (Btu/(hr oF ft)). The HI outer tube is also made from stainless steel. I had considered using aluminum since it is easier to work, but it has a thermal conductivity of about 120 (Btu/(hr oF ft)) which is 6 times higher than stainless steel. I want the heat to stay at the center tube so that it is available to heat the air rather than conducting the heat away and into the wood. Bare aluminum also has a nasty habit of forming an oxide layer which could make the outer tube larger in diameter and crack the wood over time. Stainless steel remains very stable and is much stronger.
I also measured a surface contact temperature of 285F at the core outer tube with 12 volts applied to the HI. Since the heat conduction path is severely limited, there will be much less heat transferred to the wood which will eliminate any charring concerns.